By Ian Baird.
Every time a report is written about the Harbour Board’s expansion plans into the Bay of Nigg, there is invariably a reference to a Scottish Enterprise report which justified the project in economic terms, along the lines of, ‘An independent study, commissioned by Scottish Enterprise, estimates that the development will generate an additional £1 billion per annum to the economy by 2035 and will create an additional 7,000 equivalent jobs.’
But that Report was written in December 2013, three and a half years ago and therefore pre-dating the current prolonged oil downturn.
Before finally committing to the project in December when a contract was agreed with Dragados, surely in the light of what is acknowledged to be a significantly changed trading environment, the assumptions and projections made in the Biggar Report should have been reviewed?
Had this been done with any vigour, it is difficult not to come to the conclusion that the business case for £350+ million development no longer stands up to scrutiny and proceeding with the development on that basis cannot be justified.
Let’s look at some aspects of the Report from the perspective of 2017.
1) Harbour Capacity: One of the most compelling arguments emanating from the Harbour Board as justification for the expansion was that the harbour was working at or near full capacity. The argument was echoed in the Report which stated:
“It is clear additional capacity is required to retain activity in the oil and gas sector in Scotland. If this capacity is not developed, then there is a risk that new and existing demand will be lost to Norway. Capacity constraints at the Harbour are also likely to hinder existing and potential users from developing new market opportunities in areas such as renewable energy, decommissioning, passenger ferries and cruise liners.”
As the construction of the expansion begins, is the existing harbour still running at or near full capacity? The Report noted that arrivals to the port in 2012 numbered in excess of 8,100. Based on the Board’s statements we have to assume this figure is close to maximum capacity. By 2014 arrivals were very similar at 7,937, but in 2015 they dropped to 7,428 and then precipitously to 6,462 in 2016 (unpublished).
That’s more than a 20% drop in traffic activity from the 2012 high to 2016. In short, the harbour is no longer working at or near to full capacity. Of course, had the arrivals levelled off at around the 8,000 mark, it could be legitimately argued that capacity issues were inhibiting expansion but with a 20% drop in activity it is clear that this is quite simply a downturn in business.
To update, the first 4 months of 2017 are no better than the equivalent period last year; and so just as the heavy plant moves in to the Bay, annual arrivals are around 1600 fewer per year than when ‘at or near maximum capacity’.
When challenged about declining arrivals at the 2016 AGM, Chief Executive Colin Parker argued lost business because of larger vessels being unable to enter the harbour were the main cause of the decline. This seems a curious statement given that vessels as large as 20,000 tonnes have used the harbour and yet the average gross tonnage is only about 4,000 tonnes. Two of the largest ships using the harbour are the passenger ferries plying to the Orkney and Shetland Isles. They each have a gross tonnage of 11, 720.
How many arrivals were there of vessels with a gross tonnage of over 10,000 tonnes, other than the ferries, using the port in a year? In 2015, only 21 out of 7,428, or .002%; in 2016, ever fewer at 11. Apart from the ferries, the upper 50% of the tonnage capacity range (10,000 to 20,000 tonnes) is virtually unused.
Where is the evidence that lack of size capacity is inhibiting business?
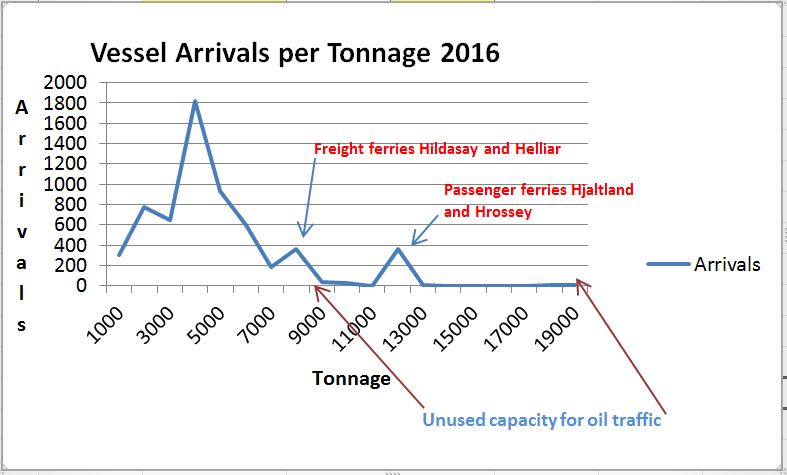
Fig. 1: The Harbour Board claims the existing harbour is too small for larger vessels. This graph shows that, apart from passenger and freight ferries running to the Northern Isles, the upper end of the tonnage capacity range from 7000 tonnes upward is barely utilised by oil-related, cargo or other vessels.
2) The new market opportunities identified in the Report – renewable energy, decommissioning, passenger ferries and cruise liners – are central in the projections of increasing traffic to the expanded facility. How well does potential success in these markets stand up to scrutiny from today’s perspective? Let us look at each in turn:
Renewable Energy: Despite initial enthusiasm for chasing business in this market, the Harbour Board has been very quiet about prospects in this sector since the Report’s publication.
There has probably been a belated recognition that weaknesses in the local infrastructure (inadequate roads network for heavy and wide loads, lack of fabrication facilities) and being close to neither centres of turbine and blade manufacture nor to the offshore areas identified as potential for offshore wind arrays, means that there are no specific advantages, and several disadvantages, for suppliers of renewable energy components considering using Aberdeen as a transport base.
Biggar suggests a need for creating industry clusters around key infrastructure investment locations, and that one such cluster should incorporate the supply chain for offshore renewables by developing the land beside Nigg Bay as a marine renewable cluster in Aberdeen City and Shire.
Fine words, but despite the fact that construction of the harbour expansion is under way, there seems little action towards this suggested initiative and there seems inadequate land available to develop a suitably well-equipped cluster as proposed.
Decommissioning: Although the total decommissioning market is huge, Aberdeen’s potential to handle significant elements of it will again be limited by onshore infrastructural weaknesses and by the lack of deep-water berthing. Since the Report was published, many other ports in Scotland, North-east England and Norway have signalled their determination to secure a share of the decommissioning market.
Many, such as Dundee, Cromarty, Kirkwall and Scapa Flow are already well ahead in extending infrastructure and capacity. In what will be a highly competitive scramble for work, it is difficult to see Aberdeen, coming late into the game with improved facilities in 2020, attracting any more than relatively minor contracts.
Ferries: Apart from its inclusion in the Report as one of the potential markets for the expanded port, no evidence or research is offered to substantiate the sector as a potential market. The Northern Isles are the only destinations with a regular ferry service to Aberdeen. The existing ferries are large and, although running near to full capacity at peak holiday periods, for much of the year they are running well below.
At current passenger and freight usage levels, larger ferries plying those routes would not be cost-effective. NorthLink have not identified any need, nor expressed any interest, in introducing larger ferries to Kirkwall and Lerwick.
Cruise Ships: The Report predicts that up to 40 cruise ships could be attracted to the new harbour each year but there are quite a number of qualifications to that figure:
“If a new harbour is built and [if] improvements are made to surrounding roads infrastructure then this may make the harbour a more attractive destination for visiting ships. For example road improvements may make it easier for coaches to access to the quayside, which would make it easier for cruise companies to organise excursions for passengers. The additional space may even make it possible to create dedicated visitor reception facilities. [My emphasis]”
The projection of 40 cruise ships per annum is therefore very speculative. While it is true that the average size of cruise ships is rising, ruling out many of them from the opportunity of docking in the existing harbour, it does not follow that a sufficiently large harbour will attract those larger ships. A bigger swimming pool doesn’t necessarily mean more (or larger) swimmers, perhaps just more space per swimmer.
If we compare the new harbour with, for example, Shetland’s port at Lerwick, which is projected to attract 80 cruise ships in 2018, there must be some doubt about its attractiveness as a destination, requiring as it will a bus journey with views (and possibly smells) of a sewage works, possibly an incinerator, Altens industrial estate and a complex onward route to get to either Aberdeen city centre or to Deeside.
In fact, all of the Report’s projections of future economic gains are qualified by the recognition that for their predictions to be realised it would be necessary ‘to upgrade the roads infrastructure in the surrounding area’.
We are now embarking on a £350 million development, not only in the absence of any such planned upgrade, but with the economics of the North Sea oil industry considerably changed for the worse, and with technological changes and innovations which lessen Aberdeen’s ability to attract certain kinds of business (for example the commissioning of the Pioneering Spirit vessel which can lift and transport complete platform topsides of up to 48,000 tonnes to a limited number of deep-water berths).
There is no doubt that on the completion of the new harbour, some additional types and sizes of vessels will visit the port.
The question is: will they do so in sufficient numbers and frequency to justify a £360 million investment and the permanent loss of a valuable amenity to the local community?
To fulfil the expectations of the Biggar Report, harbour activity not only has to regain the current 20% loss of traffic but has to utilise to near capacity the additional 25% berthing the expansion will enable. That’s 45% above current activity.
Given that the mainstay of the harbour is oil-related business and that it is not contested that it is an industry in decline, there must be a huge question mark over the prediction that in Year 20 of the Report’s projections the net economic impact of Aberdeen Harbour in the City and Shire will be 12,350 jobs and £1.8 billion GVA (Gross Value Added).
The questions are these therefore. What re-evaluation of the Biggar Report was undertaken prior to the final decision to proceed with the expansion into the Bay of Nigg? Is anyone from the Harbour Board, Biggar Economics or Scottish Enterprise prepared to stand by the projections in the 2013 Report? If not, on what basis is the project proceeding?
Sources: Economic impact of Aberdeen Harbour Nigg Bay Development – A final report to Scottish Enterprise, Biggar Economics, December 2013
- Comments enabled – see comments box below. Note, all comments will be moderated.